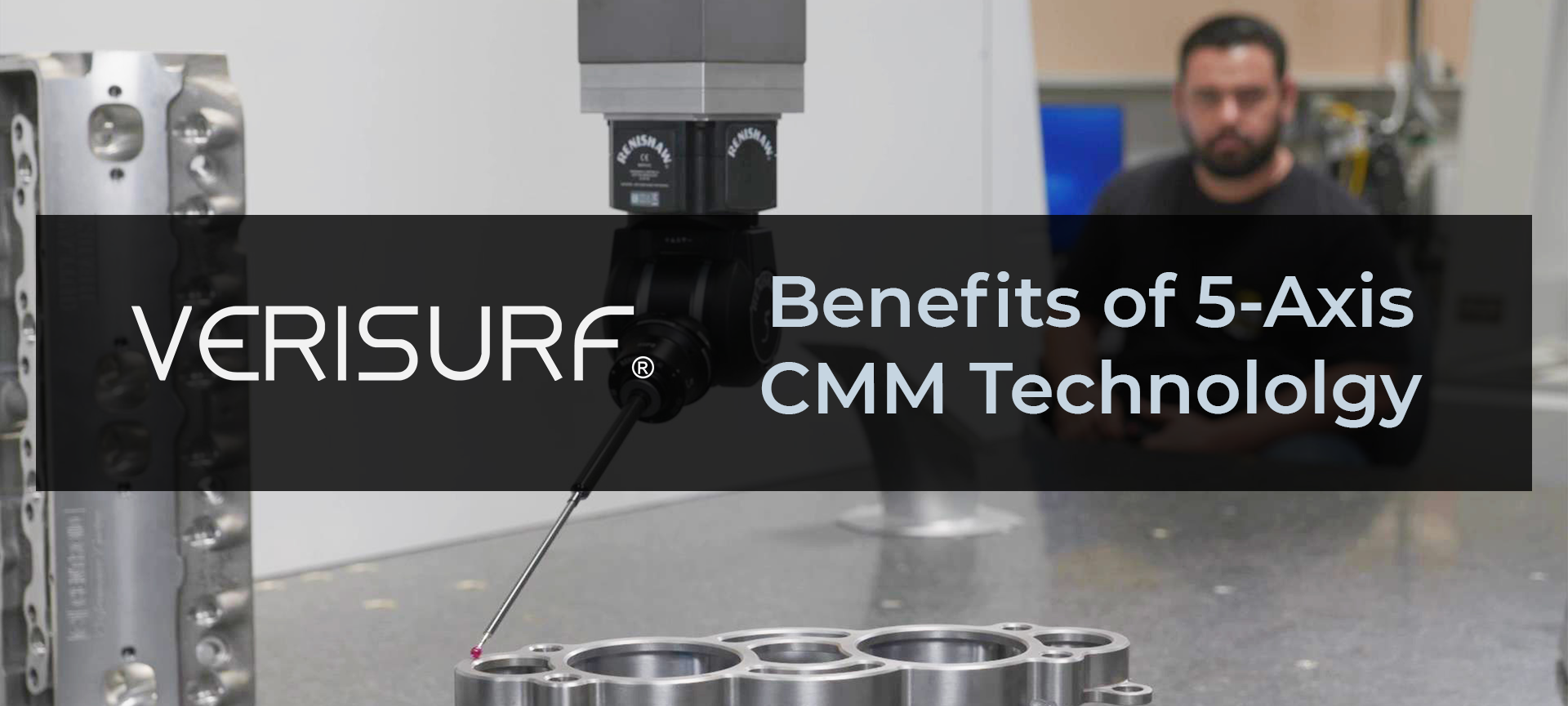
Benefits of 5-Axis CMM Technology
Coordinate measuring machines (CMMs) are the most common 3D measurement systems used to inspect manufactured parts, especially when precision is needed. Whether for first-article or in-process inspection, or ongoing quality control, CMMs are the preferred solution. Since their inception, CMMs have been a somewhat consistent design employing three axes of highly restricted, controlled, and tracked movement. In more recent times, two axes of rotation have been added via the probe head, also tightly restricted, controlled, and tracked, giving CMMs a total of five axes of precision motion control.
Video courtesy Renishaw
For 3-axis machines, the necessary probe angles to access feature measurements are achieved by indexing the head in fixed increments to the desired angles. This can be done manually by hand or automated with a servo motor, typically controlled by the part inspection program. For 3-axis systems, the X, Y and Z moving sections provide the motion necessary to drive the probe to its programmed trigger points, while the probe is held at a fixed angle for triggering. With newer 5-axis technology, in addition to the three axes of movement, the head provides two more axes via pivoting, motorized joints in the head itself. Having the three primary axes of the machine working in concert with the two rotational axes of the head, a perfect symphony of five axes of movement becomes available. The resulting 5-axis, advanced probing system provides numerous functional and productivity benefits.
5-Axis Time Savings
- HIGHER SPEEDS – With the technical advancements offered by active probe triggering from head rotations, 5-axis enables higher running speeds and therefore lower cycle times while avoiding accuracy and repeatability penalties.
- INFINITE POSITIONING – The control system includes automatic calibration routines for both the head and the probe. Once these routines are completed, the head can be used in any position with any probe. This guarantees optimal feature access minimizing stylus changes
- INFERRED CALIBRATION – Unlike 3-axis systems with indexing heads that require time-consuming probe calibration for each angle in the part program, the 5-axis system extrapolates the probe calibration with accurately inferred calibration for all angles, thereby providing huge time savings.
- LESS TIME REORIENTING THE PART – With better angles and greater freedom for feature entry and probing, there is a reduced need to reorient the part during a cycle.
- LESS PROGRAMMING TIME – Less programming time due to the limitations of feature access with 3-axis programming.
Time Comparison
3-Axis System Versus 5-Axis System1
5-Axis Operating Cost Savings
- REDUCED OR ELIMINATED SPECIAL FIXTURING – Infinite positioning and improved access to features allow for the elimination or reduction of the need for special fixturing.
- MACHINE LONGEVITY – Five-axis offers more life and less maintenance for wear components due to the reduction in machine movement.
Greater Accuracy at Higher Speeds1
Renishaw makes a very precise and understandable description of the speed-accuracy benefits of 5-axis:
“Traditionally, there’s been a speed versus accuracy compromise when it comes to coordinate measurement machine inspection. Some CMMs can move pretty fast, but when it comes to scanning a part feature, they’re slowed right down to minimize any dynamic errors associated with the inertia of the large machine elements. This counteracts any of the potential cycle time gains made by having a fast machine.
CMMs would employ either a 3-axis or a 5-axis management system. There are some significant differences between the two. With a 3-axis system, the faster you move, the more dynamic errors are introduced to the system. This is because measurement data can only be collected by moving the three axes of the machine, and the inertial forces caused by the acceleration and deceleration of the machine’s structure introduce detrimental effects on the performance accuracy of the system.
Five-axis technology, which is only available from Renishaw, moves the X, Y, Z of the machine and the A & B of the head simultaneously. So instead of driving the machine at high speeds and accelerations, machine motion can be smooth and continuous whilst leaving the head to do most of the work. Over the lifetime of a CMM, the loads placed on the moving elements of the machine are much less detrimental to its performance.”1
5-Axis CMM Provides Easy Access to Features at All Angles
For certain inspection articles, some features, or at least the full extent of them, can be challenging to reach for CMM probing. Typical indexed probes used by 3-axis CMMs can usually reach the depths of features, but often with difficulty. It can depend on the use of special probes, re-fixturing the part multiple times, and increasing the cycle time.
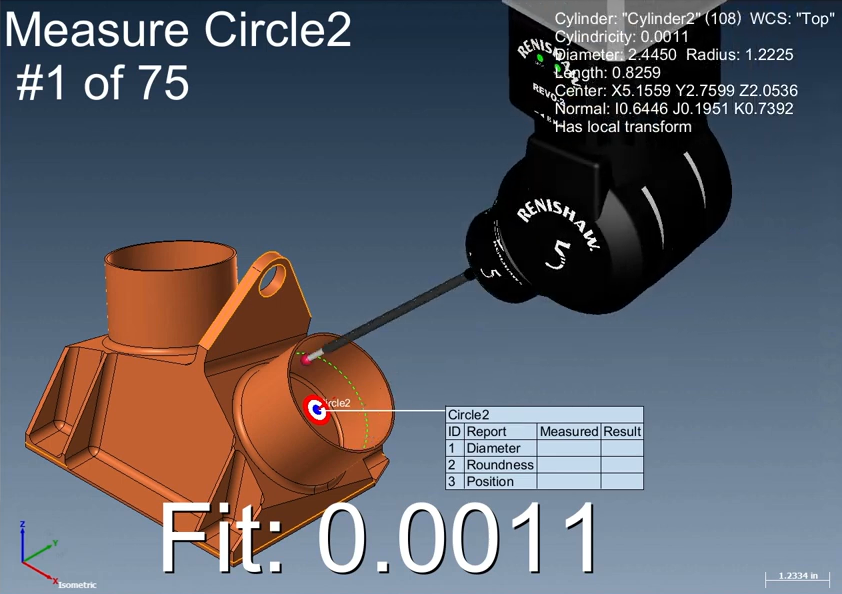
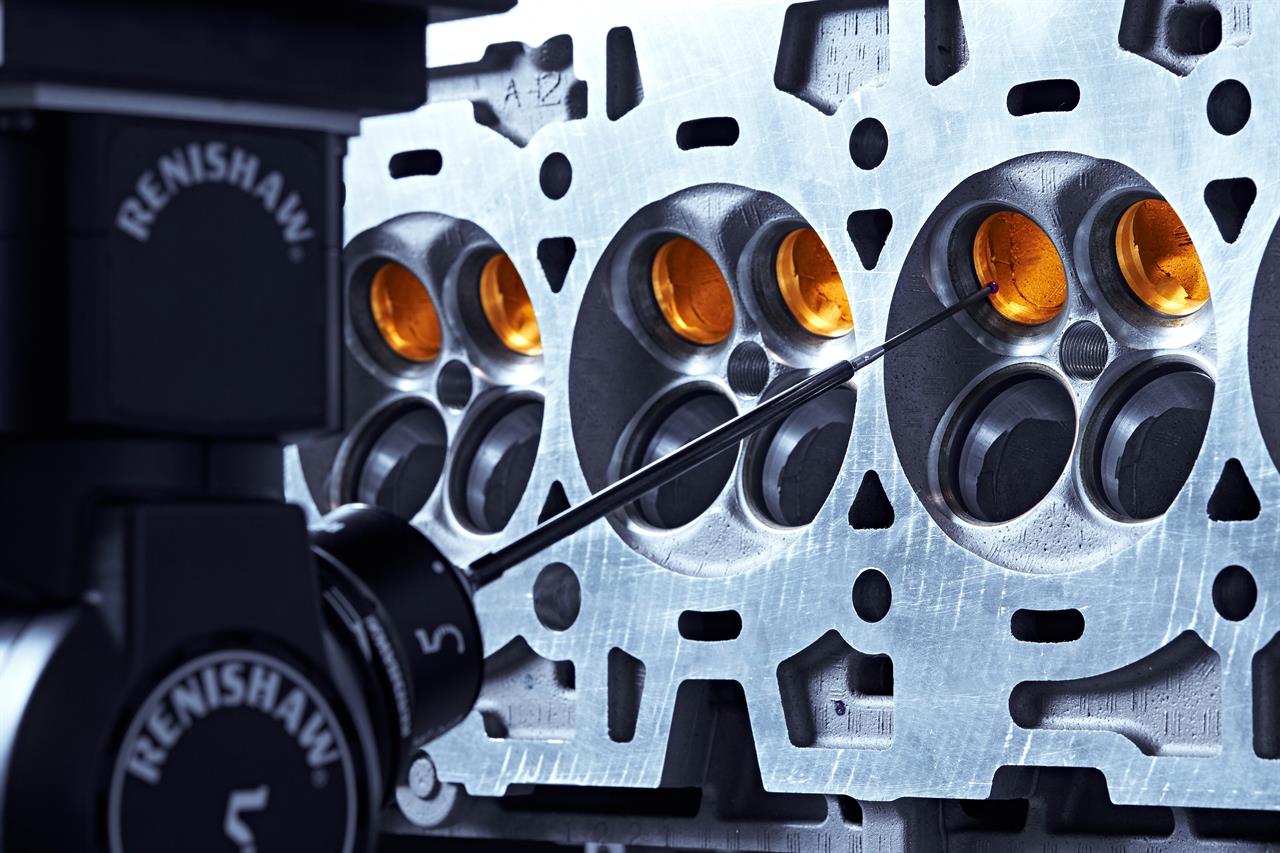
When programming for 5-axis probing, it is simple to align the probe’s entry vector with the feature. The CMM program, along with the 5-axis control system, will then make a clean entry into the feature and begin probing using primarily head movement, while minimizing movement of the CMM’s major structures.
Modern CMM programming solutions such as Verisurf Software – widely recognized as top coordinate measuring software, make it easy to set entry and exit vectors for features. Verisurf’s Custom Clearance feature provides intuitive, real-time graphical guidance and adjustment, ideal for 5-axis probe paths.
Verisurf Custom Vector’s intuitive translucent sphere guidance tool is used to easily direct the entry and exit clearance vectors while the sphere diameter represents the entry and exit distance.
Technology
The 5-Axis “Head Touch”
At the core of 5-axis systems is a probing technique called the head touch. While 3-axis probing engages the touch-trigger probe by moving the machine’s major X, Y and Z elements in unison to contact the part, 5-axis probing uses mainly head movement to trigger points.
Unlike conventional touch-trigger measurement methods which rely on speeding up the motion of the CMM’s 3 axes to measure quickly, HEAD TOUCHES utilize head motion to minimize the dynamic errors of the CMM at higher measurement speeds.
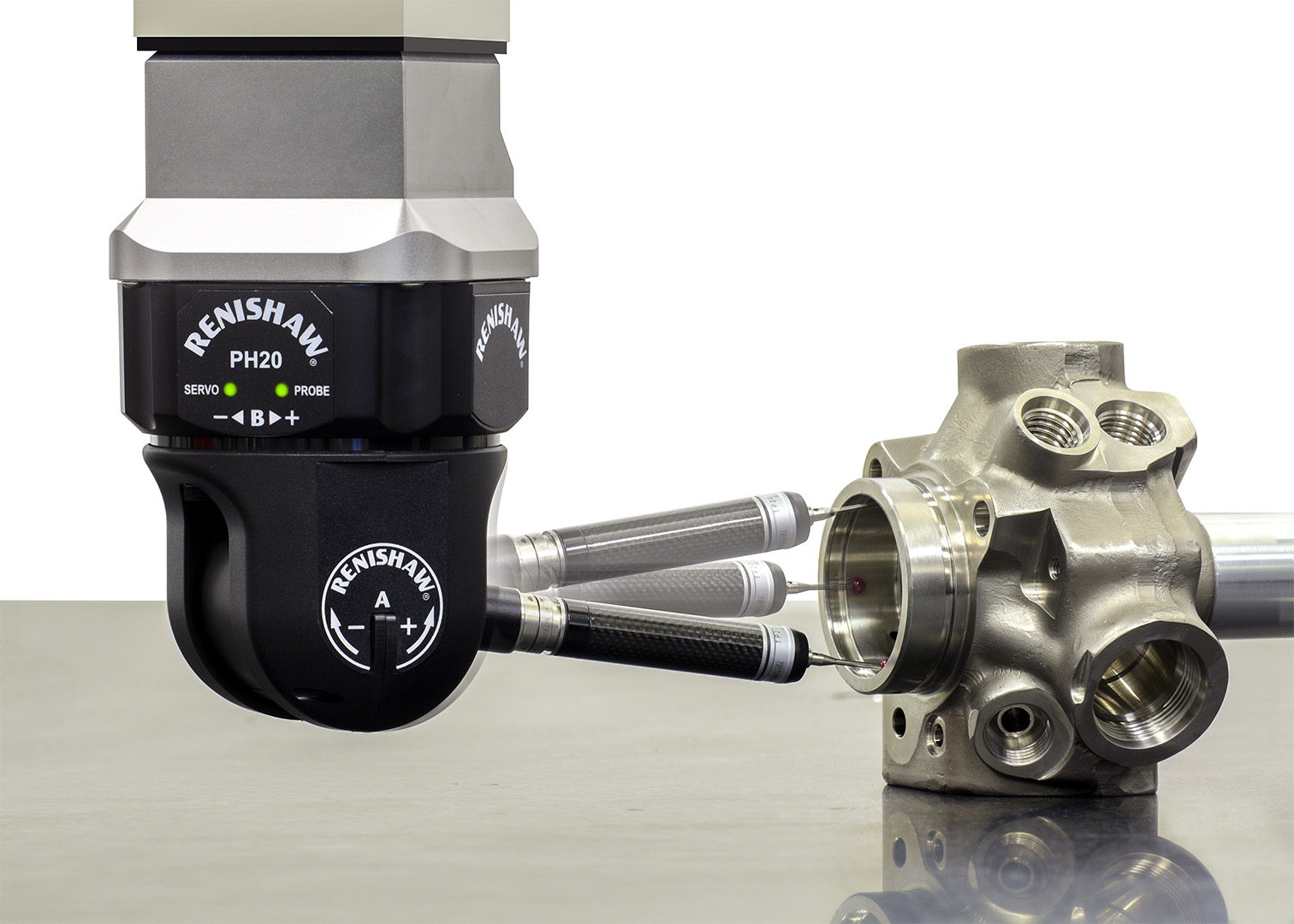
HEAD TOUCHES allow measurement points to be taken by rotating the head’s A and B pivot joints, minimizing or eliminating movement of the CMM structure. Points can be taken faster, and with improved accuracy and repeatability.1
Infinite Positioning
Infinite positioning is an aspect of 5-axis CMM probing technology that provides increased productivity, greater flexibility in job setup, and better use of the CMM’s working volume. Furthermore, it guarantees optimal feature access minimizing stylus changes.
Using air bearings allows the head to move freely without friction. Furthermore, the control system includes automatic calibration routines for both the head and the probe. Once these routines are completed, the head can be used in any position with any probe. The probe automatically aligns itself with the part coordinate system helping to avoid collisions and some of the headaches that might come from excessive fixturing positions of the part.1
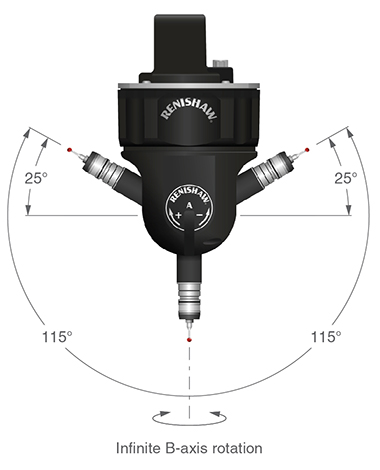
Inferred Calibration
Inferred calibration is one of the productivity benefits that comes from 5-axis CMM probing technology of the Renishaw REVO® and PH20 systems.
The technique, developed originally for the PH20 determines the head orientation and probe position in a single operation, allowing subsequent measurement at any head angle. After initial probe calibration, additional probe tip modules only require a few touches on the calibration sphere before use. Enhanced metrology performance is available if needed by calibrating the probe tip at the feature orientation.1
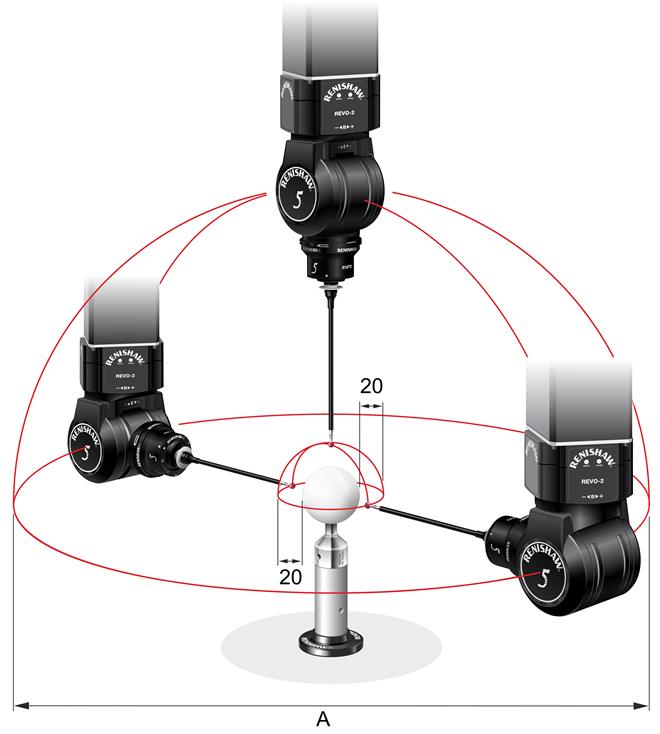
Extra Productivity from Custom 5-Axis Techniques
Verisurf unique measurement techniques improving the speed and accuracy of 5-axis enabled CMMs.
Verisurf Custom Techniques
Verisurf Curve Scan – Curve scan is available only from Verisurf and automates the measurement and reporting of small transitional surfaces and edges like fillets and chamfers used to reduce sharp edges and stress concentrations. Learn more.
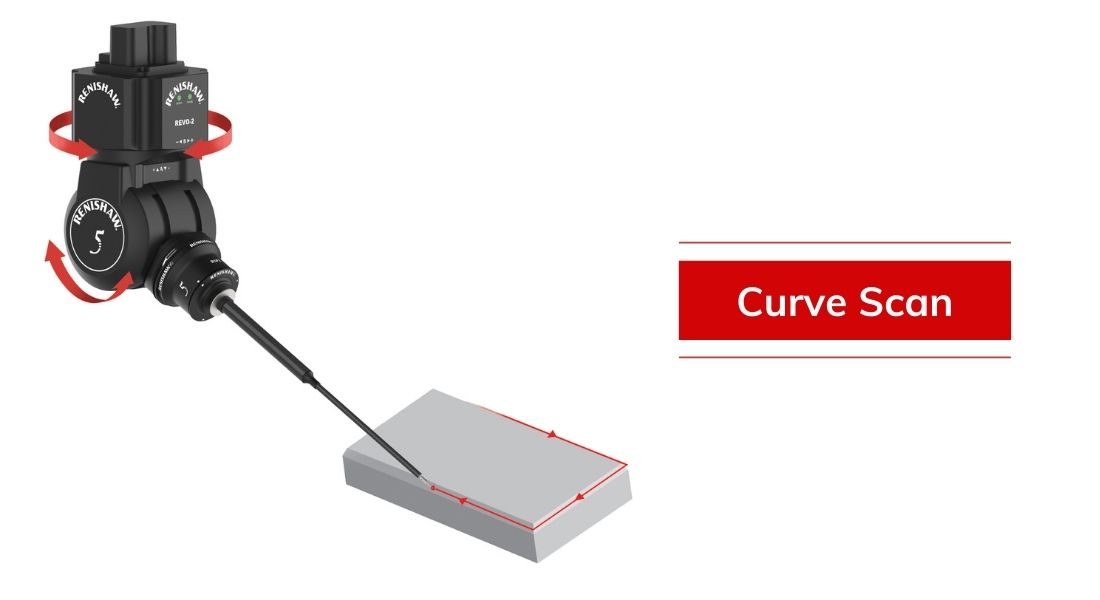
Verisurf Pocket Scan – Pocket scan is available only from Verisurf and is used for rapid and automated inspection of isogrid and orthogrid structures that stiffen and save weight on aerospace panels and pressure vessels. Learn more.
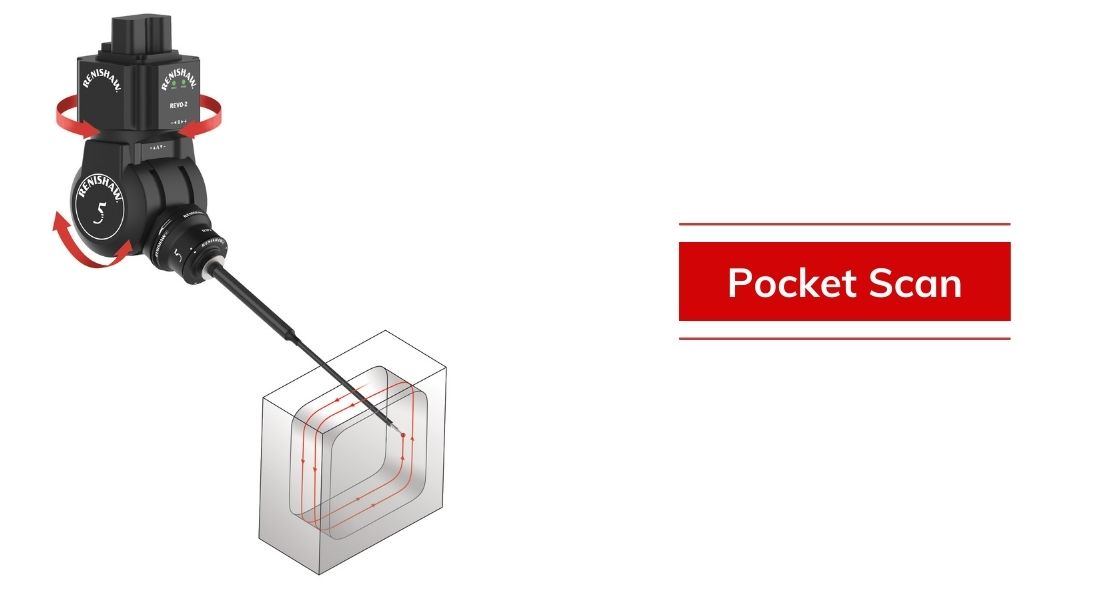
Verisurf Spiral Scan – Spiral scan is available only from Verisurf and enables CMM programmers to accurately and quickly, program and measure turbine blade or propeller surfaces while staying clear of neighboring blades. Learn more.
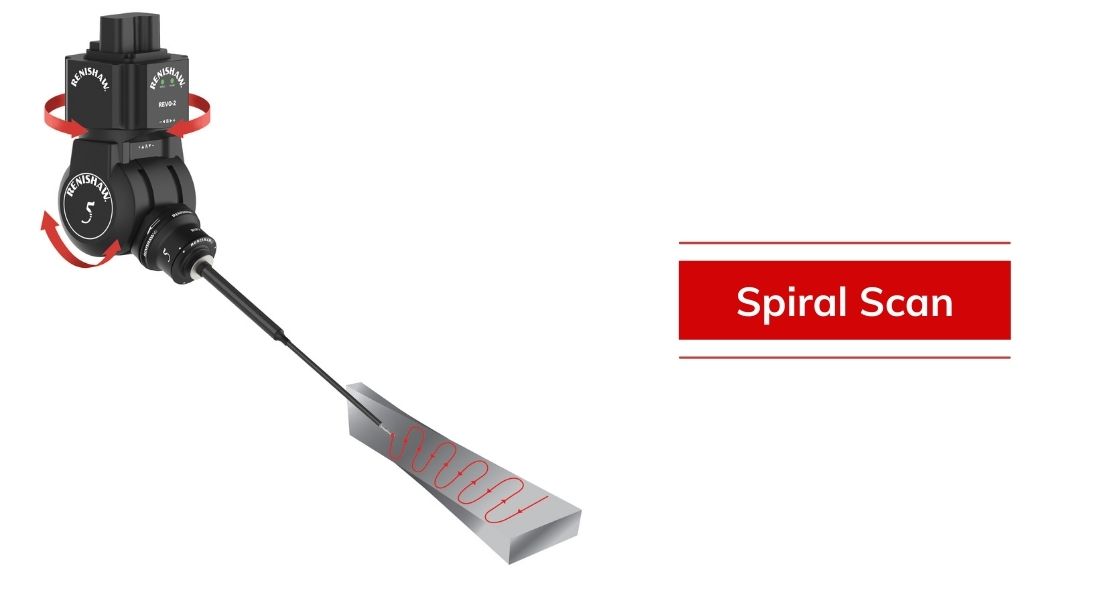
Standard Techniques (Learn More)
Circal Scan
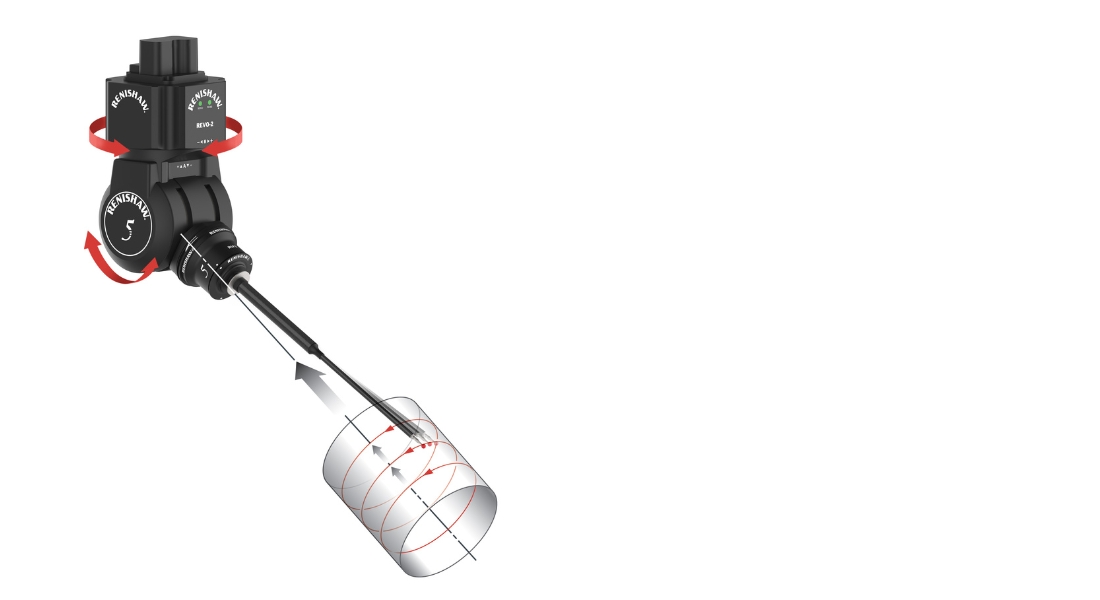
Edge Scan
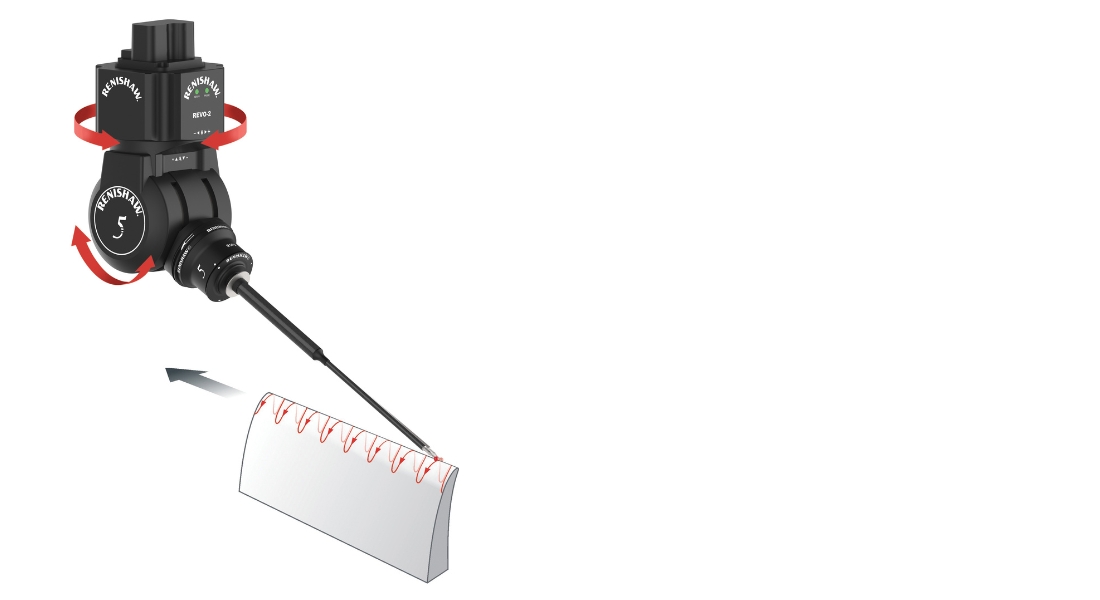
Surface Sweep
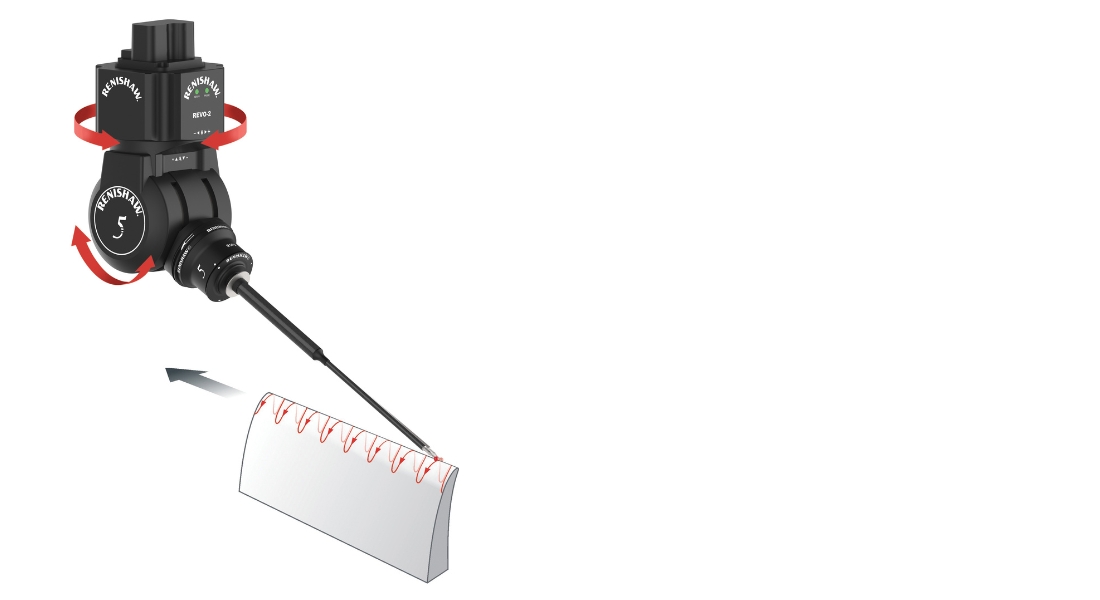
Gasket Scan
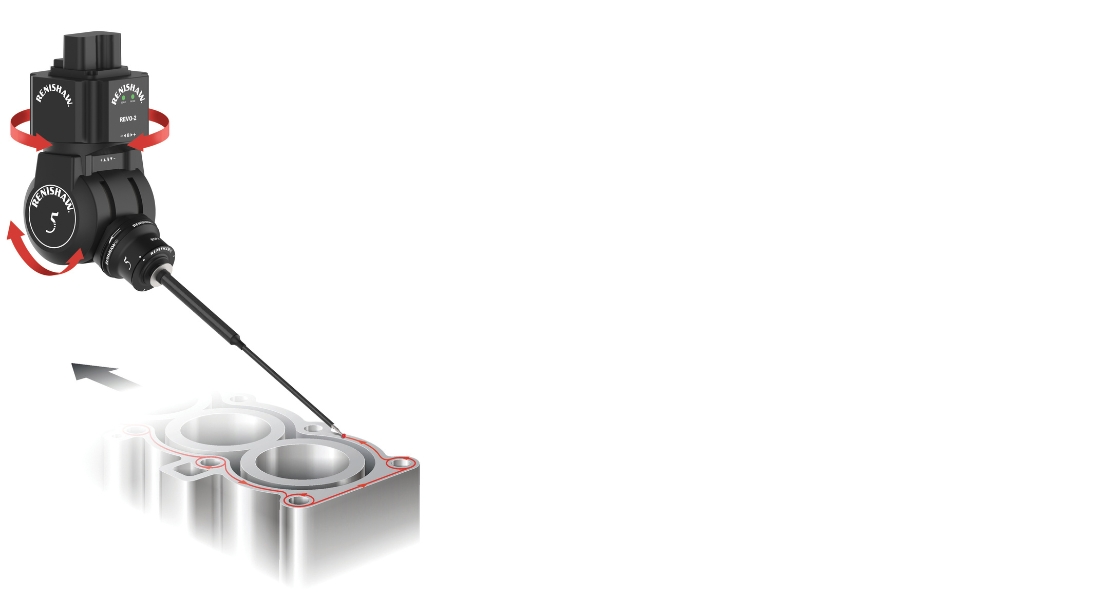
Helical Scan
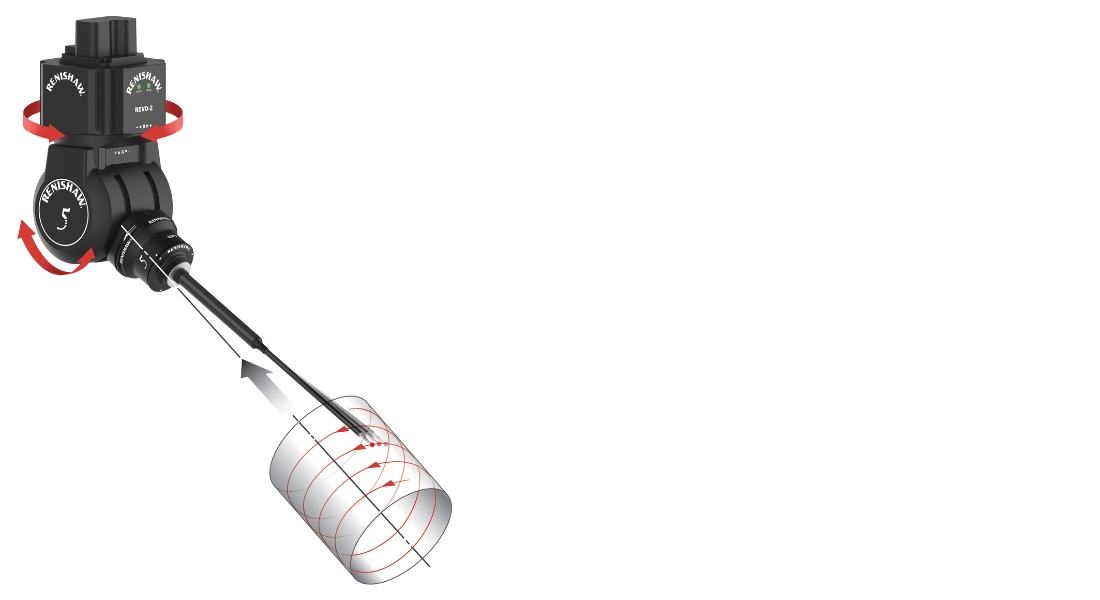
Head Touches
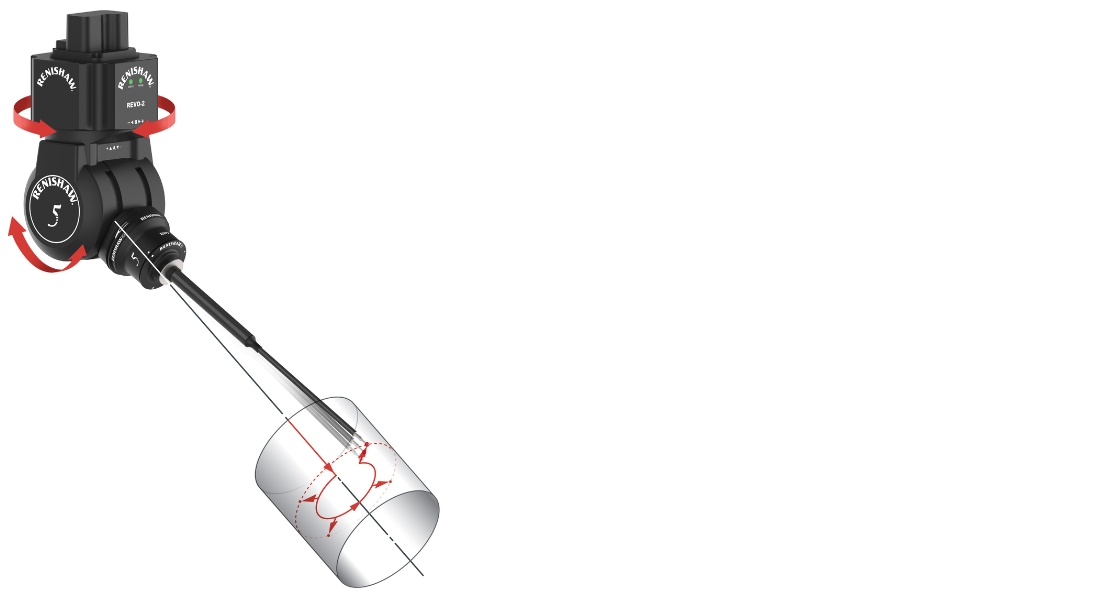
Advanced 5-Axis Sensors
Renishaw REVO® RVP
Vision Probe
- 5-axis non-contact structured light measurement of complex surfaces
- Automatic exposure compensation for a variety of materials and colors
Renishaw REVO® RUP1
Ultrasonic Probe
- Automated 5-axis ultrasonic thickness measurement
- 1 mm to 20 mm thickness measurement range
- 10 micron or better accuracy using touch points
REVO® SFP2
Surface Finish Probes
- Significant time savings and reduced part handling
- Access to difficult to measure holes and pockets
- Surface finish integrated measurement reports
At Five-Axis Industries, 5-Axis Machining Paired with 5-Axis Metrology is Perfect for Efficiency and Productivity
Five-axis is in their name, so it should not be a surprise to know the company has been using 5-axis machining capabilities for more than 20 years. Machining complex shapes and features such as propellers and other helically shaped parts is easier and more accurately machined using 5-axis technology. This is due to continuous 5-axis movement, which produces better results on contoured or curved shapes. 5-axis machines are also easier to set up with fewer clamp changes, and you can typically access five sides of a part with a single setup. These and other benefits of 5-axis machining are clear and have pushed the adoption of the technology among shops at a rate of 7% compounded annual growth in recent years.
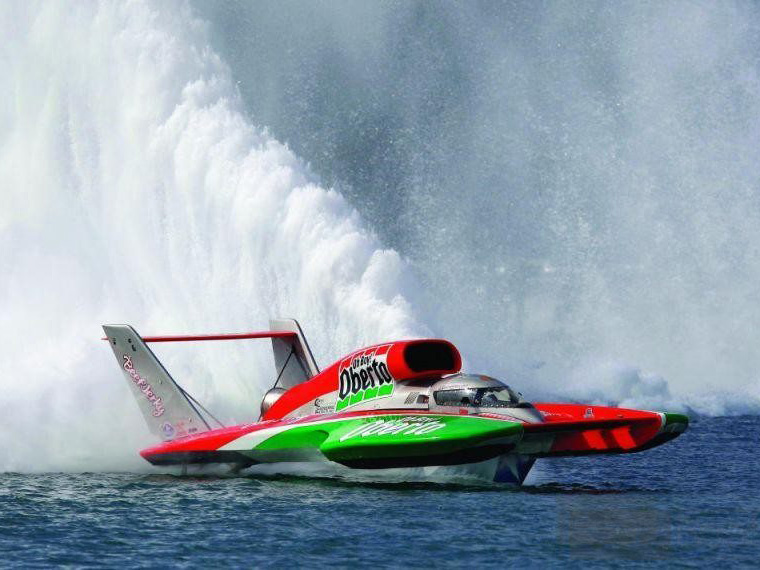
“For us, 5-axis capabilities are all about moving the part less and articulating the machine to move around the part. We were an early adopter of 5-axis machining; finally, CMMs have caught up and can offer the same productivity gains in measurement and inspection. 5-axis workflow from machining through quality verification just makes common sense. We realize up to 50% reduction in overall cycle time plus added flexibility using 5-axis machining; the time savings are comparable to inspection using our 5-axis CMM, powered by Verisurf.” Full story: Five-Axis Industries
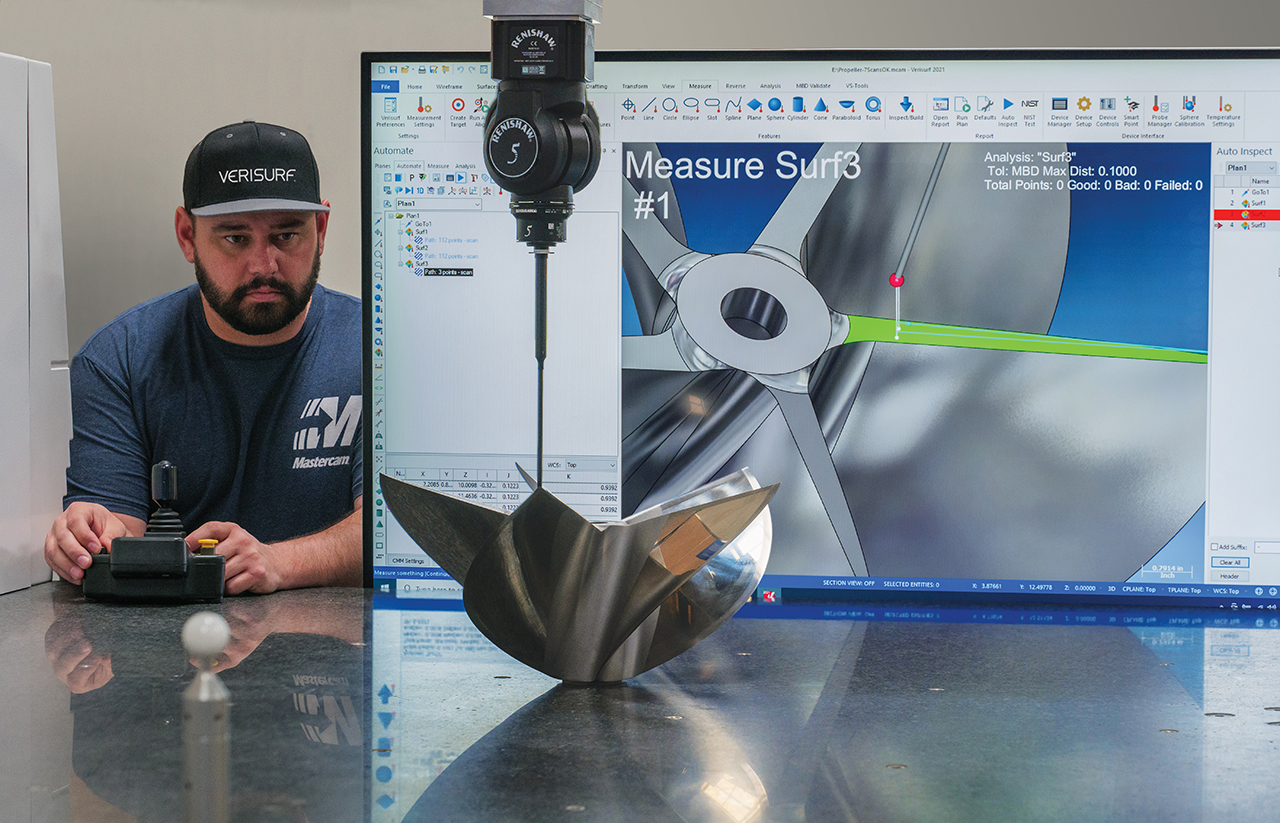
Is a 5-Axis CMM System Right for Your Shop?
If your shop workload is high enough that saving time in precision CMM inspection helps you to cut costs and maintain a higher throughput, then 5-axis CMM systems could make the difference you are looking for. For small shops performing low-volume work or machining simple shapes, 3-axis systems are likely a more economical fit. For companies looking to modernize and stay ahead of the technology curve, and when they are willing to invest in high performance, 5-axis may be a good choice.
The cost of 5-axis touch probing systems is modestly higher than 3-axis systems, and 5-axis tactile scanning systems come at a relatively significant initial capital outlay. However, a good return on investment can be relatively quick for those handling higher volumes and more complex work. The ability to impress customers and new prospects with innovative technology is likely to help secure new business.
Whether it is 5-axis or conventional 3-axis CMM technology that fits your needs better, be sure to pair it with modern programming, analysis, and process optimization software to get the most out of your investment.
Frequently Asked Questions About 5-Axis CMM Technology
What is the main difference between 3-axis and 5-axis CMM probing?
Three-axis CMMs use their three main, moving structures (X,Y & Z) to move the touch-probe for measuring. Five-axis systems add two additional movements of the probe head, rotating about the Z axis element and a variable probe angle, which are moved to trigger points.
What are the main benefits of 5-axis over 3-axis CMM probing?
Five-axis systems enable higher-speed probing while maintaining accuracy. Three-axis systems require slower probing speeds to hold accuracy, due to the inertia of the heavy moving elements of the main structures, causing distortion under acceleration.
Are there other benefits of 5-axis?
Five-axis systems experience less machine wear on the major motion elements, as the head performs a significant portion of the work. Access to features is improved, so parts require less re-fixturing, specialized fixtures, or probes to measure features.
Does a 5-axis cost more?
Five-axis systems are more expensive than 3-axis, indexing head systems. Advanced systems, such as the Renishaw REVO, which enable tactile scanning and long probes, require a considerable initial investment compared to 3-axis. However, there is a considerable return on investment since 5-axis provides reduced cycle times and lower machine maintenance.
References:
1www.renishaw.com
Author: Scott Knoche – Verisurf Software, Inc. (technical marketing & sales at Verisurf since 2002)